In the realm of custom product creation, few items hold as much potential for personalization and creativity as the humble mug. From cherished family photos to witty slogans, sublimating onto mugs allows businesses to transform ordinary drinkware into cherished keepsakes. However, achieving flawless results requires a keen understanding of the sublimation process, along with careful consideration of materials, design, and the crucial element of heat.
The first step in mastering mug sublimation is selecting the right type of mug. While ceramic mugs are the most commonly used substrate for sublimation, not all ceramic mugs are created equal. Mugs with a smooth, white coating provide the best surface for vibrant and long-lasting prints. The smooth surface allows the sublimation ink to adhere evenly, resulting in sharp, detailed designs. Matte or textured finishes, on the other hand, may produce less predictable results, as the ink may not fully penetrate the surface or may appear muted upon transfer.
Once the mug substrate is chosen, attention turns to the design itself. High-resolution images are essential for achieving crisp and clear prints. Whether it’s a family portrait, company logo, or intricate pattern, the quality of the design will ultimately determine the quality of the finished product. Additionally, it’s important to consider the size and placement of the design in relation to the mug’s dimensions and handle position. Designs that wrap around the entire mug or span across multiple sides require careful alignment to ensure a seamless transition.
Preparation is key to successful mug sublimation. Before applying the design, the mug must be thoroughly cleaned and prepped to remove any dust, oils, or residue that may interfere with the sublimation process. Using a lint-free cloth and a mild detergent, wipe down the surface of the mug and allow it to dry completely. This ensures that the sublimation ink adheres evenly to the surface, minimizing the risk of imperfections or inconsistencies in the final print.
The sublimation process itself involves transferring the design from a specially coated transfer paper onto the surface of the mug using heat and pressure. The transfer paper is printed with the desired design using sublimation ink, which is then placed against the surface of the mug and secured in place with heat-resistant tape. The mug and transfer paper are then placed in a heat press, where they undergo a precise combination of heat and pressure to activate the sublimation ink and transfer the design onto the mug.
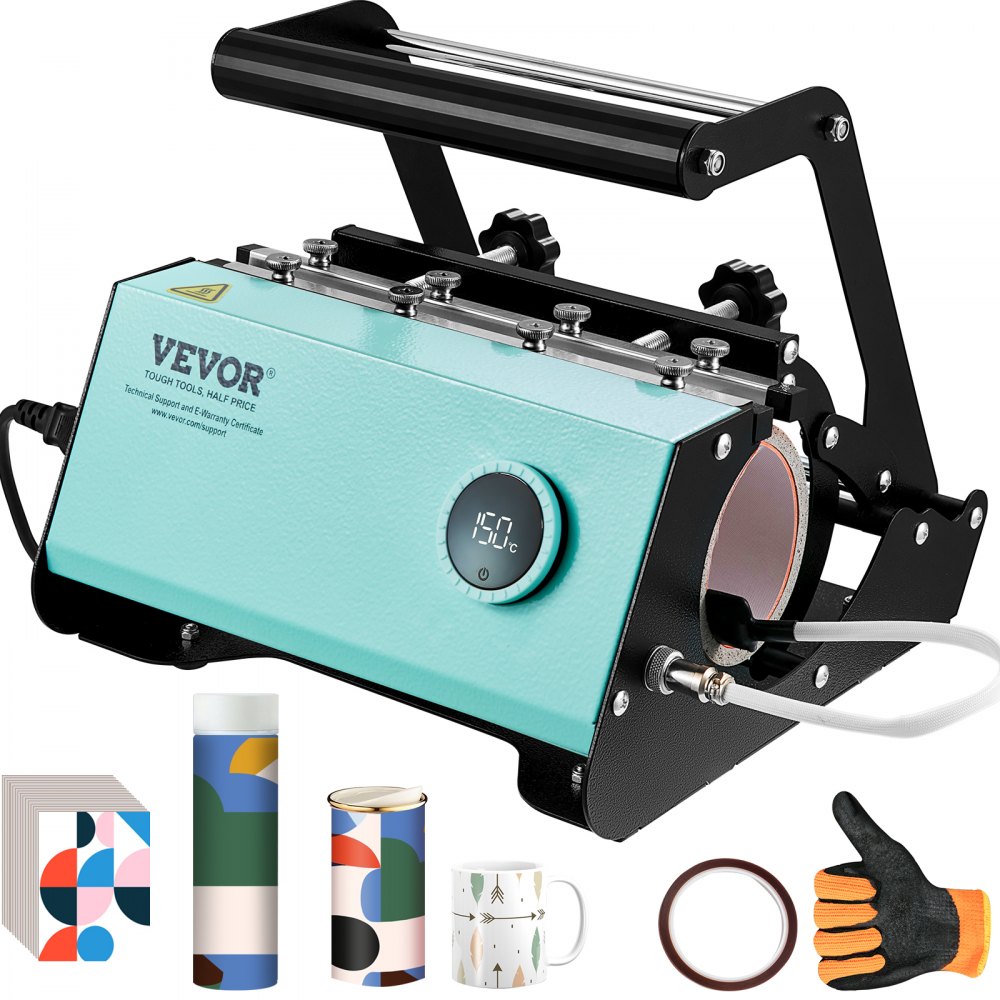
Timing and temperature are critical factors in achieving optimal results. Most mugs require temperatures between 150 to 200 degrees Celsius applied for 100 to 200 seconds. Too much heat or pressure can cause the ink to bleed or fade, while too little may result in incomplete or uneven transfer. Additionally, different types of mugs may require slightly different settings to achieve the desired outcome. It’s essential to consult the manufacturer’s guidelines and conduct thorough testing to determine the ideal parameters for each specific mug and design.
Once the sublimation process is complete, the mug must be allowed to cool before handling. This ensures that the design sets properly and adheres to the surface of the mug. After cooling, the mug can be inspected for any imperfections or defects and, if necessary, touched up or reprinted as needed.
In conclusion, mug sublimation is a nuanced and intricate process that requires careful attention to detail and precision, especially regarding the application of heat. By selecting the right materials, preparing the surface properly, and mastering the sublimation technique, businesses can create custom drinkware that delights customers and stands the test of time. Whether it’s a personalized gift for a loved one or branded merchandise for a corporate event, mug sublimation offers endless possibilities for creativity and expression.